Exploring the transformative realm of automotive manufacturing reveals a fascinating shift propelled by the innovative power of 3D printing technology. In the realm of modern production, the marriage of 3D printing and automotive manufacturing has sparked a revolution, reshaping traditional processes and pushing boundaries. As an expert in the field, I’ve witnessed firsthand the profound impact of 3D printing on the automotive industry, revolutionizing design, prototyping, and production with unparalleled efficiency and customization. This article delves into the disruptive influence of 3D printing on automotive manufacturing, shedding light on the evolution of this dynamic partnership and its implications for the future of the industry.
The Evolution of 3D Printing in Automotive Manufacturing
Exploring the evolution of 3D printing in automotive manufacturing showcases a journey marked by innovation and transformative impacts. As an expert in the field, I delve into the intricate developments that have shaped the partnership between 3D printing technology and the automotive industry. This collaboration has not only revolutionized traditional processes but has also paved the way for enhanced efficiency and customization within automotive manufacturing.
Early Adoption and Experiments
In the nascent stages of integration, automotive manufacturers embarked on a journey of exploration and experimentation with 3D printing technology. This phase was characterized by a spirit of innovation as industry pioneers sought to leverage the capabilities of additive manufacturing for prototyping and small-scale production. The early adopters of 3D printing in automotive manufacturing laid the groundwork for future advancements, setting the stage for rapid progress in the field.
Major Milestones Achiejsonaled
Throughout its development, 3D printing in automotive manufacturing has achieved significant milestones that have reshaped industry standards and practices. From the production of intricate components to the customization of vehicle parts, additive manufacturing has demonstrated its versatility and efficiency. Major breakthroughs in material sciences, software integration, and printing techniques have propelled the automotive industry into a new era of manufacturing possibilities, marking a transformative journey that continues to evolve.
Technological Advancements in 3D Printing
Exploring the Technological Advancements in 3D Printing within the Automotive Industry, we witness a fundamental shift in manufacturing processes.
Materials Used in Automotive 3D Printing
In Automotive 3D Printing, materials play a pivotal role in achieving desired outcomes. Metals like aluminum, titanium, and steel are commonly utilized for their strength and durability. Polymers such as ABS and PLA find application in creating prototypes and functional parts due to their cost-effectiveness and versatility. By integrating advanced materials like carbon fiber composites, manufacturers enhance the structural integrity of components, ensuring higher performance standards and lightweight designs.
Innovations in Printing Techniques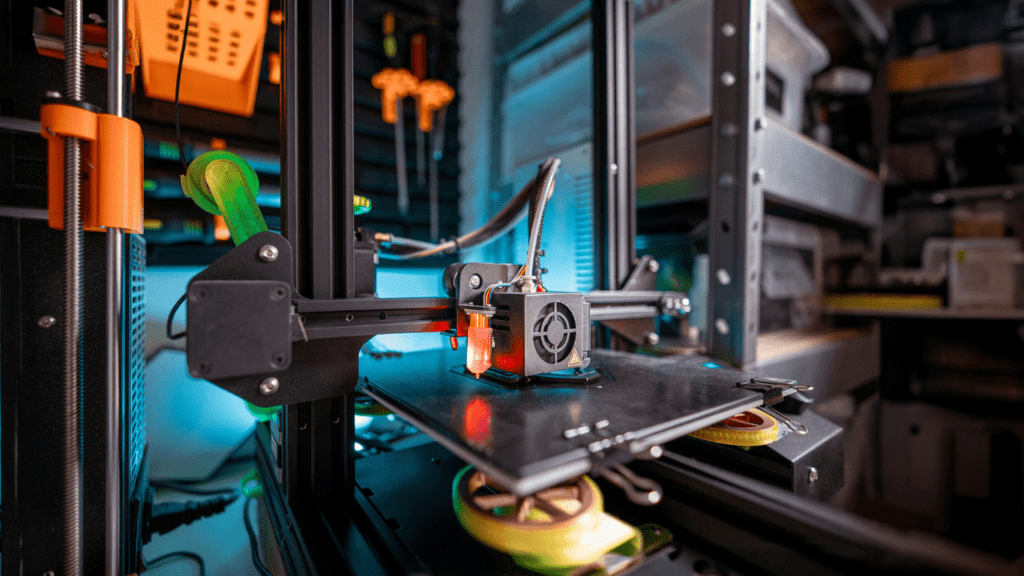
Innovations in Printing Techniques have revolutionized the Automotive Manufacturing landscape. Additive Manufacturing processes like Selective Laser Sintering (SLS) and Fused Deposition Modeling (FDM) enable intricate part production with high precision. Continuous advancements in Multi-Jet Fusion (MJF) and Stereolithography (SLA) systems have accelerated production speeds while maintaining product quality. The adoption of Hybrid Manufacturing, combining traditional methods with 3D printing, enhances efficiency and customization capabilities, shaping the future of automotive production.
Impact on Car Production Processes
3D printing has revolutionized car production processes, offering a myriad of benefits that enhance efficiency and flexibility in manufacturing.
- Reducing Prototyping Time
I have found that 3D printing significantly reduces prototyping time in automotive manufacturing. With the ability to create rapid prototypes directly from digital designs, manufacturers can quickly iterate and test various components before final production. This streamlined process saves valuable time compared to traditional methods, where prototyping could take weeks or months. - Customization and Complex Designs
In my experience, 3D printing enables unparalleled customization and intricate designs in the automotive industry. Manufacturers can tailor components to specific requirements with ease, allowing for bespoke parts tailored to individual models or even customers. The flexibility of 3D printing empowers designers to unleash creativity and produce complex geometries that traditional manufacturing techniques struggle to achieve. This level of customization sets a new standard for personalization in car production, catering to diverse consumer preferences.
Environmental and Economic Benefits
I’ll now elaborate on how 3D printing positively impacts both the environment and the economy within the automotive manufacturing sector.
Reduction in Waste Production
3D printing significantly reduces waste production in automotive manufacturing. Unlike traditional subtractive manufacturing methods, 3D printing is an additive process where material is deposited layer by layer. This additive approach results in minimal material wastage as only the required amount of raw material is used to create the final product. For instance, in traditional manufacturing, excess material is often removed during machining processes, leading to higher levels of waste. With 3D printing, the sustainability of the production process is enhanced, contributing to a more environmentally friendly manufacturing approach.
Cost Efficiency for Manufacturers
3D printing offers cost efficiency for manufacturers in the automotive industry. By reducing material waste and streamlining production processes, 3D printing helps minimize overall production costs. The ability to create complex geometries and customized parts with 3D printing means manufacturers can optimize designs for efficiency, resulting in lighter and more durable components. Moreover, the flexibility of 3D printing allows for on-demand production, eliminating the need for large inventories and reducing storage costs. The cost-effective nature of 3D printing makes it an attractive option for automotive manufacturers looking to enhance efficiency and reduce operational expenses.
Challenges and Limitations
Moving forward in the realm of 3D printing in automotive manufacturing, there are certain challenges and limitations that need to be addressed for broader adoption and seamless integration within the industry.
Technical Challenges in Printing
Incorporating 3D printing into automotive manufacturing processes poses technical challenges that require innovative solutions. One significant challenge lies in ensuring the structural integrity of 3D-printed parts, especially in critical components such as engine parts or safety features. The need for rigorous testing and certification processes to meet industry standards is paramount in overcoming these technical hurdles. Additionally, optimizing printing speeds without compromising quality remains a challenge that industry players are actively working on to enhance production efficiency.
Acceptance in the Industry
Despite the transformative potential of 3D printing in automotive manufacturing, widespread acceptance within the industry is still evolving. One of the key hurdles is the perceived high initial investment costs associated with implementing 3D printing technologies on a large scale. Convincing traditional manufacturers to adopt additive manufacturing as a viable alternative to conventional methods requires showcasing the long-term cost savings, production flexibility, and quality improvements offered by 3D printing. Moreover, ensuring compatibility with existing manufacturing processes and supply chains presents another challenge that needs to be addressed to facilitate seamless integration of 3D printing in automotive manufacturing workflows.
Future Trends in Automotive 3D Printing
Predictions and Upcoming Technologies
As the automotive industry continues to embrace 3D printing, I anticipate several exciting advancements on the horizon. One key prediction is the increasing use of metal 3D printing for producing complex car parts with high strength and durability. This shift towards metal additive manufacturing will enable the creation of lighter yet stronger components, enhancing vehicle performance and fuel efficiency.
Another upcoming technology that holds promise in automotive 3D printing is the development of multi-material printing capabilities. This innovation will allow manufacturers to integrate different materials within a single part, opening up new possibilities for hybrid materials with unique properties. By leveraging multi-material 3D printing, car makers can enhance structural integrity, create parts with varying levels of flexibility, and reduce the overall weight of vehicles without compromising on strength.
Integration with Other Manufacturing Innovations
As automotive manufacturing evolves, the integration of 3D printing with other cutting-edge technologies is set to revolutionize the industry. One significant trend to watch out for is the incorporation of artificial intelligence (AI) and machine learning algorithms into the 3D printing process. By harnessing AI-driven design optimization and predictive modeling, car manufacturers can streamline the production of intricate components, improve material selection, and enhance overall manufacturing efficiency.
Furthermore, the synergy between 3D printing and automation technologies is paving the way for fully digitalized and lights-out manufacturing facilities in the automotive sector. Automated processes, such as robotic post-processing and assembly, coupled with 3D printing capabilities, will not only accelerate production cycles but also ensure consistent quality control and precision in manufacturing. This seamless integration of automation with 3D printing is poised to drive significant cost savings, minimize human error, and elevate the scalability of automotive production lines.